진동식 볼 피더 keep production lines moving, making part feeding systems efficient and automated. They’re a key part of bowl feeder automation, helping industries handle small components with precision. But like any machine, they can run into issues. One of the most common? Overheating. If left unchecked, it can slow production, wear out components faster, and even damage the feeder itself.
Why Do Vibratory Bowl Feeders Overheat?
Several factors can cause heat buildup in vibratory parts feeders:
- Motor Overload– When the feeder takes on more than it’s designed for, or if internal circuits malfunction, the motor has to work harder. That extra effort generates excess heat.
- Long Run Times– Running the feeder non-stop without breaks can cause heat to build up, especially if there’s no cooling system in place.
- Poor Heat Dissipation– The temperature rises quickly if the system doesn’t get proper ventilation.
- Friction and Wear– Springs, bearings, and other moving parts in bowl feeder systems wear down over time. More friction means more heat.
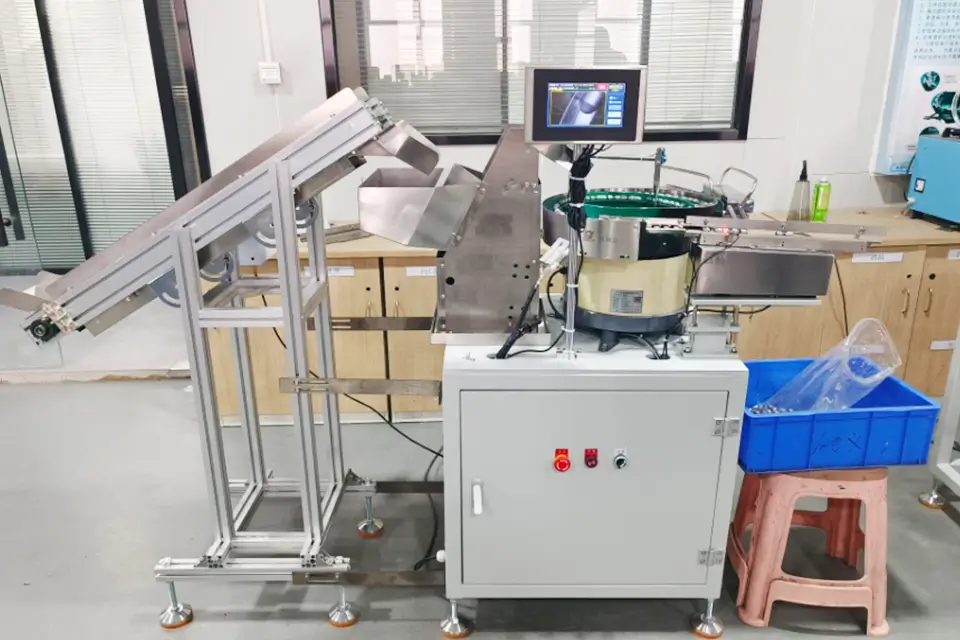
How to Prevent Overheating in Vibratory Bowl Feeders
To keep your part feeding systems running smoothly, take these steps:
- Keep an Eye on Motor Load– Don’t push the feeder beyond its rated capacity. Regularly inspect the motor to catch any issues early.
- Improve Cooling– Add cooling fans or even a water-cooling system to help manage heat.
- Stay on Top of Maintenance– Lubricate moving parts and replace worn-out components before they start causing problems. Less friction means less heat.
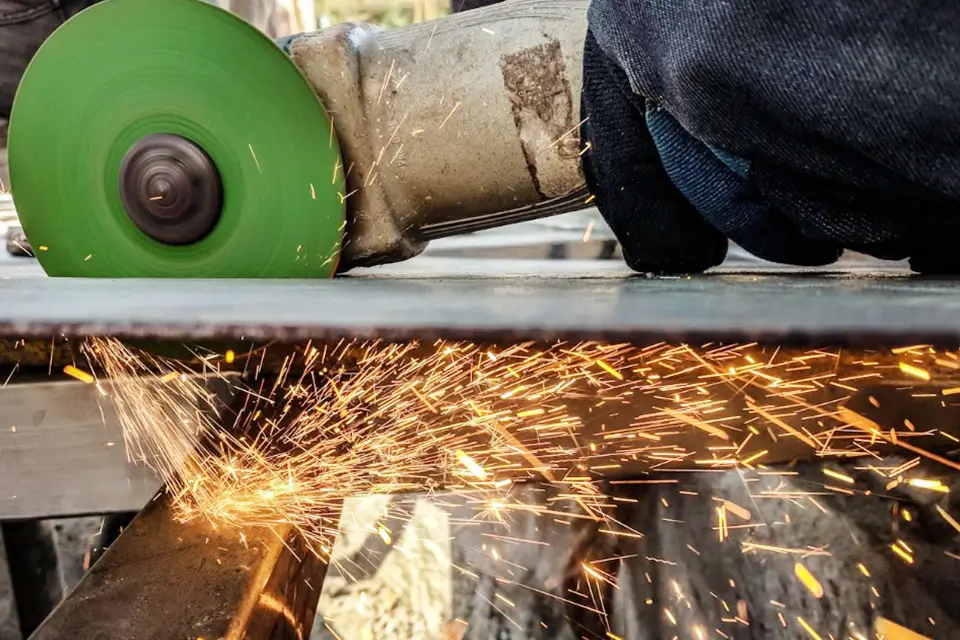
마지막 생각
A well-maintained vibratory bowl feeder stays efficient, reliable, and productive. By tackling overheating head-on, you extend its lifespan and keep operations running smoothly. Don’t wait until a minor issue turns into a major repair—regular maintenance and smart cooling solutions will save you time and money.