- Introduction
- The Challenge: Cap Feeding in Bulk
- Understanding the Design Requirements
- Designing a Pharmaceutical-Grade Vibratory Feeder
- Meeting Speed and Precision Requirements
- Manufacturing with a Focus on Hygiene
- Delivering Results on Time
- Building Long-Term Partnerships
- Applications Beyond Caps
- Conclusion
Introduction
Delivering precision and efficiency is critical in the pharmaceutical industry. This case study showcases how a vibratory feeder system was designed to handle caps, ensuring sterility and high-speed operation. With a turnaround time of 10 weeks, the system exceeded the client’s expectations, achieving a production rate of 228 parts per minute while maintaining stringent pharmaceutical-grade standards.
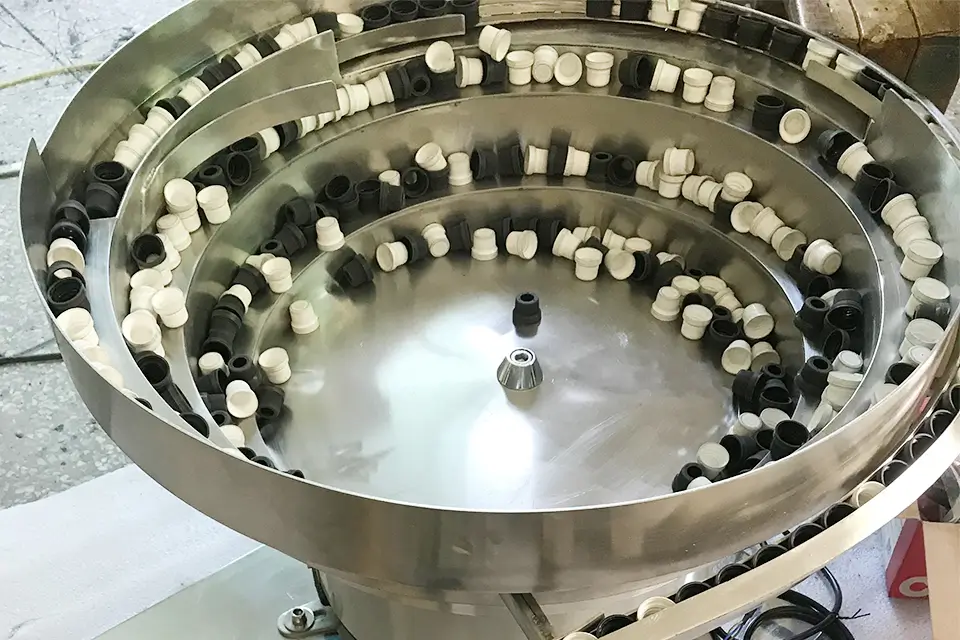
The Challenge: Cap Feeding in Bulk
Pharmaceutical manufacturers often face challenges in managing bulk components. The task was to develop a vibratory feeder system capable of taking caps from bulk, orienting them in a consistent position, and feeding them into a continuous motion capping machine. The requirement was clear: reliability, sterility, and speed were paramount.
Understanding the Design Requirements
The pharmaceutical industry demands adherence to strict hygiene and precision standards. For this project:
- Sterility: The feeder had to be designed using a fill-and-grind manufacturing method to eliminate cavities where bacteria could grow.
- Speed: The system must feed caps consistently at 228 parts per minute.
- Reliability: A seamless integration with the continuous motion capping machine was essential.
Designing a Pharmaceutical-Grade Vibratory Feeder
The Swoer Feeder Company approached the project with meticulous attention to detail. Stainless steel was chosen for its durability and compatibility with the sterile environment. The design incorporated features such as:
- Quick Dump Mechanism: To streamline the removal of excess parts.
- Polished Finish: A fill-and-grind finish to meet sterility standards.
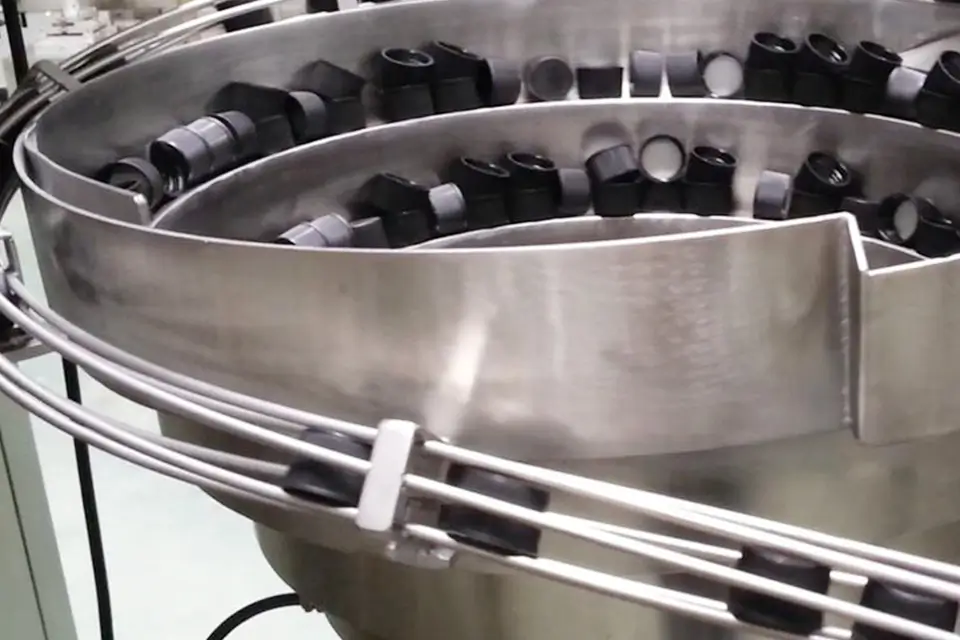
Meeting Speed and Precision Requirements
Achieving the target of 228 parts per minute demanded precise engineering. This included:
- Custom Tuning: Ensuring the vibratory feeder consistently met the speed requirements.
- Orientation Accuracy: Advanced mechanisms were employed to orient each cap in a repeatable position for seamless integration into the capping machine.
Manufacturing with a Focus on Hygiene
Maintaining sterility was a priority during manufacturing. The team implemented a fill-and-grind method early in the process, ensuring no cavities were left for bacterial growth.
- Accessible Design: Builders incorporated features for easy access during grinding and polishing.
- Final Touches: Each component was thoroughly inspected to meet pharmaceutical hygiene standards.
Delivering Results on Time
The system was delivered to the client in the Czech Republic within 10 weeks, meeting both the deadline and performance expectations. Key outcomes included:
- Exceeding the required rate of 228 parts per minute.
- A reliable single-line output of oriented caps.
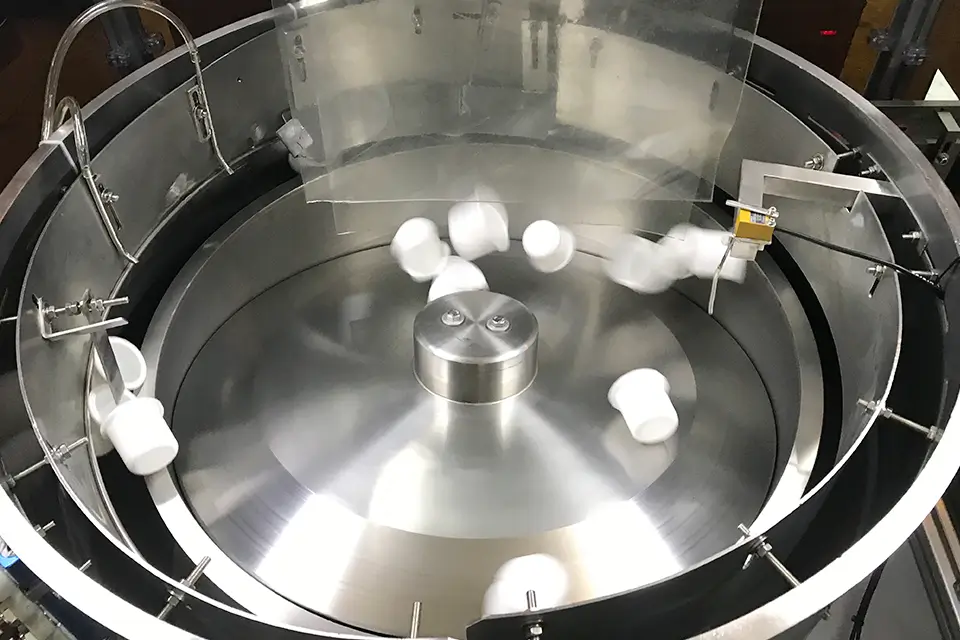
Building Long-Term Partnerships
The success of this project reinforced Swoer Feeder Company’s reputation for reliability and exceptional customer service. The client’s satisfaction led to an exclusive partnership, establishing Swoer Feeder as their trusted vibratory feeder supplier.
Applications Beyond Caps
While this case study focuses on caps, the same principles apply to other industries and products. Vibratory feeder systems can handle various components in:
- Automotive Manufacturing
- Electronics Assembly
- Medical Device Production
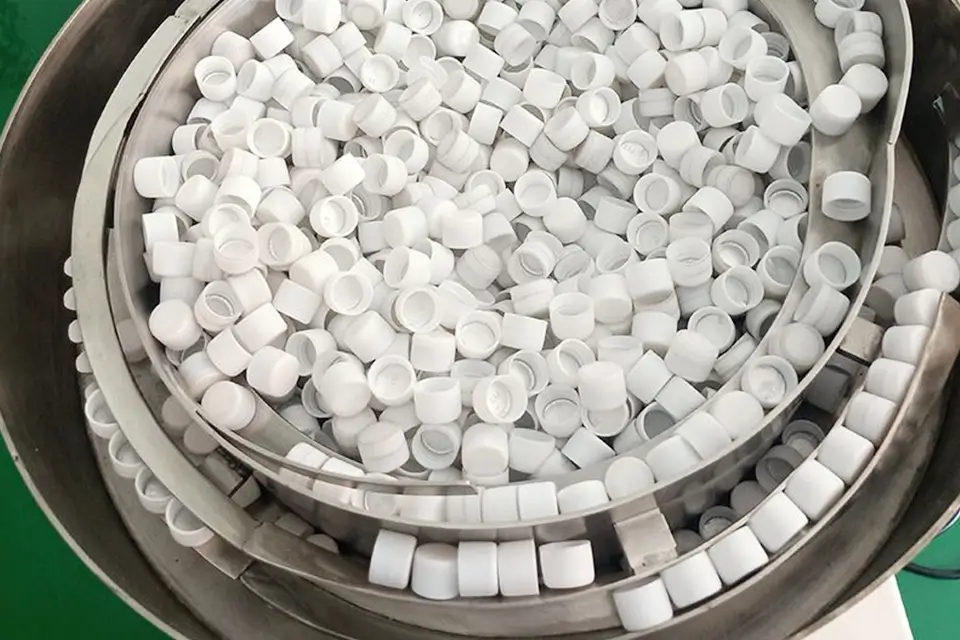
Conclusion
This project demonstrates how innovative design and precision manufacturing can meet the exacting demands of the pharmaceutical industry. From initial consultation to final delivery, the vibratory feeder system for flip-top caps showcased reliability, sterility, and speed. At Swoer Feeder Company, we remain committed to delivering quality solutions that exceed customer expectations.