- Introduction
- Vibratory Bowl Feeders: A Key Component in Assembly Automation
- Centrifugal Feeders: High-Speed Precision Feeding
- Linear Conveyor Systems: Maintaining Orientation and Flow
- Hopper Systems: Increasing Autonomy and Efficiency
- Elevators: Ergonomics and High-Capacity Storage
- Integration with Robotics and Vision Systems
- Conclusion
Introduction
In automated manufacturing, feeding systems are key to ensuring smooth and efficient assembly processes. For industries like automotive, medical devices, and electronics, having the right feeding system can greatly boost productivity, reduce downtime, and ensure accurate parts handling. This guide will explore different types of automatic feeding systems, including vibratory bowl feeders, centrifugal feeders, and linear conveyors, and explain how they can be customized to fit specific production needs.
Vibratory Bowl Feeders in Automatic Feeding Systems
Manufacturers use vibratory bowl feeders as one of the most common systems in automated assembly lines. These feeders are designed to feed parts in a controlled and efficient manner, sorting and orienting components before delivering them to the next station. Vibratory feeders are ideal for high-speed operations, providing an effective solution for bulk parts handling.
The system consists of a bowl, base, springs, and coils, which work together to create vibrations that guide parts into the desired orientation. Manufacturers can make vibratory feeders from various materials, such as stainless steel or polyamide, and apply coatings like Rilsan, epoxy, or polyurethane to prevent damage to delicate components.
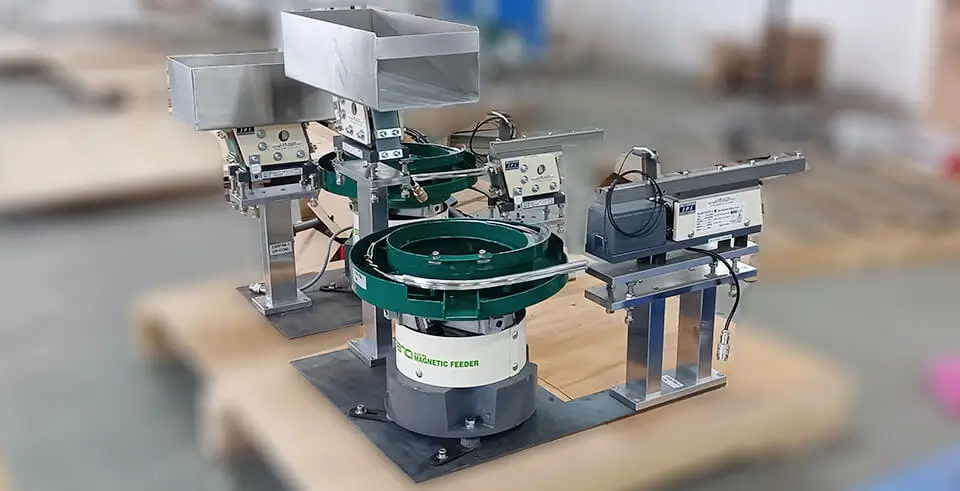
Centrifugal Feeders in Automatic Feeding Systems
For operations requiring faster and more delicate handling of parts, centrifugal feeders are the perfect solution. These systems can reach speeds of up to 1000 parts per minute, offering a rapid feeding solution without compromising on precision. The centrifugal feeder uses a rotating disc that spins at high speeds, guiding the components into position.
One of the key benefits of centrifugal feeders is that they can handle fragile or small parts, such as plastic, rubber, or metal components. They can also integrate with industrial vision systems to provide real-time feedback on part positioning, further enhancing accuracy and reliability.
Linear Conveyor Systems: Maintaining Orientation and Flow
Designers create linear conveyor systems to transport parts between different stages of the assembly process. These systems maintain the orientation of components while also serving as buffer storage to ensure a continuous flow of materials. Depending on the specific needs of your operation, linear conveyors can be vibrating rails, fluid tracks, or traditional conveyor belts.
Linear conveyors are essential for maintaining smooth transitions between different phases of the production line, particularly when handling parts that need to be fed into assembly or packaging machines. The versatility of linear feeders makes them a crucial part of any automated system.
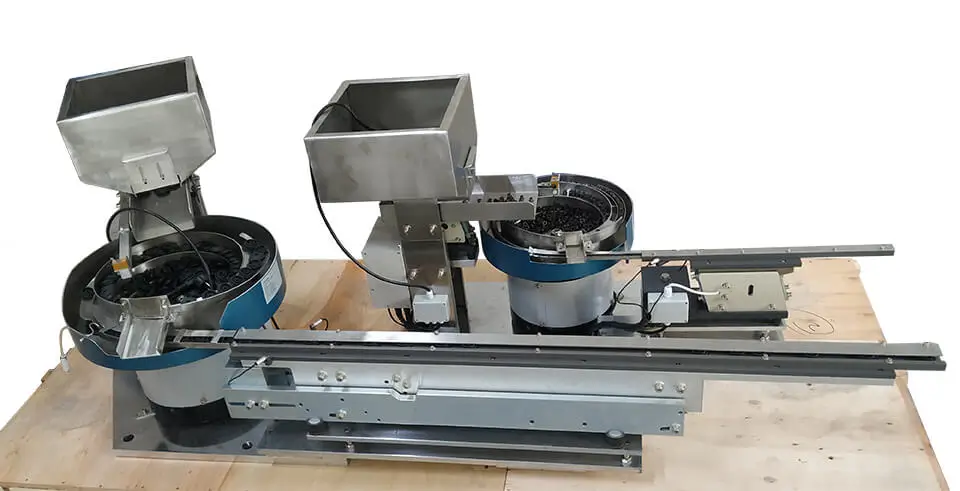
Hopper Systems: Increasing Autonomy and Efficiency
Manufacturers typically use a hopper system upstream of a vibratory or centrifugal feeder to increase its autonomy. Hoppers store large quantities of parts and feed them into the feeding system as required. They come in various sizes, ranging from 5 liters to 100 liters, and can be customized to meet specific needs.
The main purpose of a hopper system is to ensure that the feeding process remains uninterrupted by providing a steady supply of parts to the downstream systems. Designers can also create them with fixed or mobile feet for ease of use and accessibility during filling and maintenance.
Integration with Robotics and Vision Systems
The latest advancements in automation include the integration of feeding systems with robotics and industrial vision systems. This combination allows for more precise and flexible part handling, enabling robots to pick and place components with minimal human intervention.
By incorporating vision systems, robots can “see” the parts and determine their position, allowing for accurate handling and sorting. This technology is especially useful in industries where high precision and speed are crucial, such as in electronics assembly or medical device manufacturing.
Conclusion
Feeding systems form the backbone of automated assembly lines by ensuring that parts are delivered efficiently and accurately to the right stations. Whether you choose a vibratory bowl feeder, centrifugal feeder, linear conveyor, or hopper system, you can tailor each system to meet your specific needs. By integrating advanced technologies like robotics and vision systems, manufacturers can further enhance their production lines, achieving higher speeds, better precision, and improved efficiency.
Selecting the right feeding system for your business can significantly improve your production capacity and reduce operational costs.