- Introduction to Flexible Part Feeders
- Why Flexible Feeders Are the Future of Automation
- What is a Flexible Part Feeder?
- The Basics of Flex Feeders and Their Role in Automation
- Benefits of Using a Flexible Feeder
- Increased Efficiency and Flexibility
- Reduced Downtime and Operational Costs
- Flex Feeder System in Various Industries
- Automotive Manufacturing
- Plastic and Metal Processing
- Medical Equipment
- Electronics and Pharmaceutical Industry
- How Does a Flexible Feeder Work?
- Design and Functionality of Flex Feeders
- Types of Flexible Feeders
- Flex Feeder vs. Traditional Part Feeders
- Understanding Flex Trays
- Applications of Flexible Feeders
- Assembly Line Automation
- Sorting and Inspection
- Customizable Options for Flex Feeders
- Tailored Solutions for Specific Needs
- Choosing the Right Flexible Feeder
- Factors to Consider When Selecting a Feeder
- Conclusion
- The Future of Flexible Part Feeders
Introduction
Why Flexible Feeders Are the Future of Automation
In today’s fast-paced manufacturing world, automation is no longer just a luxury – it’s a necessity. Flexible part feeders are revolutionizing industries by providing a simple, yet highly efficient solution for handling and sorting parts in a variety of shapes and sizes. This technology is a game changer for companies looking to boost production, reduce human error, and optimize their processes.
What is a Flexible Part Feeder?
The Basics of Flex Feeders and Their Role in Automation
A flexible part feeder (or flex feeder) automatically sorts and organizes parts for use in various manufacturing processes. Engineers design these feeders to handle parts of different sizes and shapes with minimal adjustments. Whether it’s a screw, a small component, or an oddly shaped part, the feeder moves it from one point to another with precision. This capability makes flexible feeders an essential tool in industries that require high-speed and high-accuracy production lines, such as automotive manufacturing and electronics.
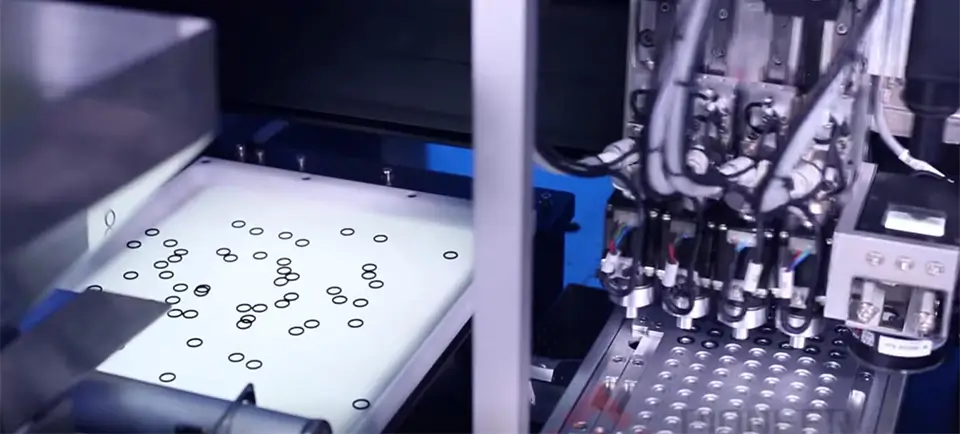
Benefits of Using a Flexible Feeder
Increased Efficiency and Flexibility
Flex feeders significantly improve both efficiency and flexibility. Unlike traditional part feeders, which manufacturers design for specific shapes and sizes, flexible feeders handle a variety of parts. They reduce the need for multiple feeders and save valuable space on the production floor. Their ability to handle different parts without constant reconfiguration minimizes downtime and ensures smoother operations.
Flex Feeder System in Various Industries
- Automotive Manufacturing: In the automotive industry, precision and speed are critical. Flex feeders help ensure that car parts, no matter how small or intricate, are fed into assembly lines with perfect alignment. By automating the part-feeding process, automotive manufacturers can ensure a faster, more reliable production process.
- Plastic and Metal Processing: Flexible feeders efficiently handle a range of parts, whether made of plastic, metal, or other materials. They perform well in industries that require precision and consistency, such as plastic injection molding or metal stamping. Flex feeders keep parts moving smoothly through production, reduce errors, and improve overall efficiency.
- Medical Equipment: The medical industry requires the utmost precision, and flexible part feeders play a vital role in ensuring that components are fed to the assembly lines without contamination or misalignment. Flex feeders can handle delicate medical parts like syringes or tiny screws for devices, making the production process safer and more efficient.
- Electronics and Pharmaceutical Industry: Flexible feeders greatly benefit these industries by handling tiny, delicate parts. Whether managing tiny circuit board components or capsules in pharmaceutical manufacturing, they place parts precisely and on time. This reduces the risk of errors and enhances overall production reliability.
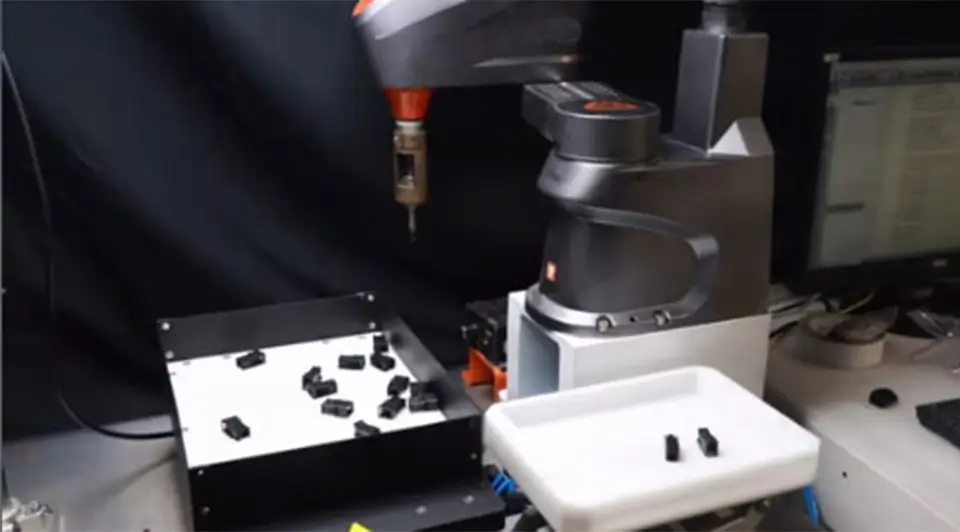
How Does a Flexible Feeder Work?
Design and Functionality of Flex Feeders
Types of Flexible Feeders
- Flex Feeder vs. Traditional Part Feeders:
- Understanding Flex Trays: Flex trays are the key to a flexible feeder’s adaptability. Engineers make these trays from flexible materials that adjust to fit various parts and feed them through the system. With proper orientation, they can handle even the most irregularly shaped parts with ease.
Applications of Flexible Feeders
- Assembly Line Automation: Flexible feeders are essential in automating assembly lines, reducing the need for manual labor and allowing for quicker, more accurate part placement. By automating the feeding process, manufacturers can ensure a steady flow of parts without interruption, making assembly lines faster and more efficient.
- Sorting and Inspection: In addition to feeding parts, flexible feeders often sort and inspect parts as they move through the production line. With integrated vision systems, these feeders can detect defects and ensure only parts that meet quality standards continue down the line.
Customizable Options for Flex Feeders
Customised Solutions for Specific Needs
Flexible feeders offer one of the biggest advantages: manufacturers can customize them to meet the specific needs of any manufacturing process. Whether adding vision systems for inspection or adjusting the tray design to accommodate a new part shape, manufacturers can adapt flexible feeders to fit the exact requirements of the production line.
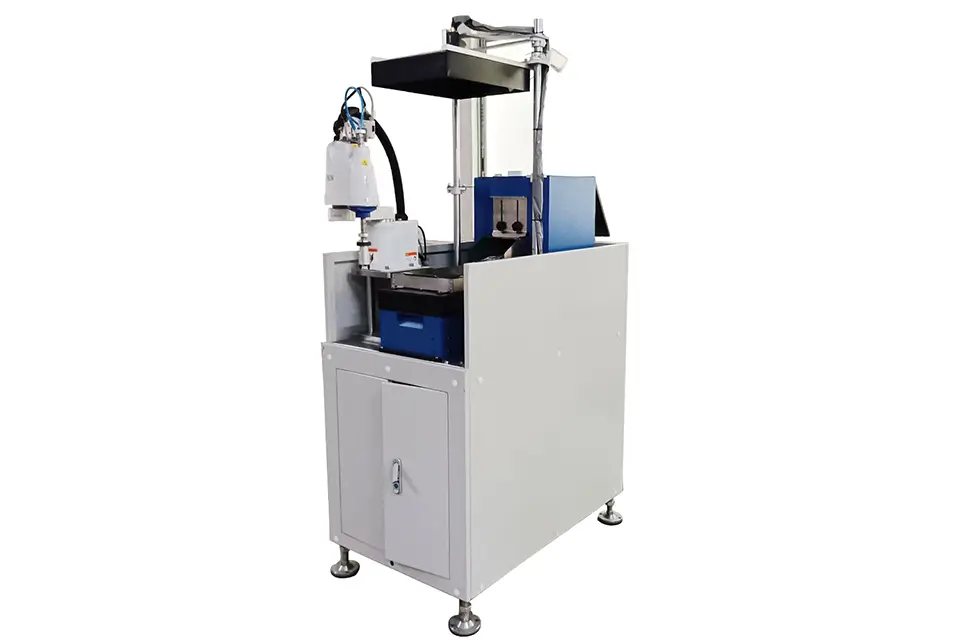
Choosing the Right Flexible Feeder
Factors to Consider When Selecting a Feeder
When choosing a flexible feeder, it’s important to consider factors like part size, shape, weight, and the specific needs of your production line. Make sure the feeder is adaptable enough to handle different parts, and consider whether additional features, such as vision systems or custom tray designs, are necessary for your process.
Conclusion
The Future of Flexible Part Feeders
Flexible feeders are here to stay, and their role in automation is only going to grow. As industries continue to seek more efficient, cost-effective solutions for part handling, flexible feeders will continue to lead the way. By reducing downtime, increasing flexibility, and improving overall production speed, flexible feeders are setting the standard for the future of manufacturing.
Contact SWOER
Communicate directly with the designer