The turntable visual screening machine is an automated inspection device designed for detecting size, appearance, and other defects in various parts. The feeding mechanism, such as a vibration plate, automatically transports parts to the glass turntable, where the visual inspection station processes images. The motion controller ensures the glass turntable rotates at a constant speed, provides encoder feedback on material position, and compares hardware positions to control the CCD camera and blowing device at multiple stations. This enables fully automated inspection and screening of appearance, size, and other aspects. The turntable visual screening machine is widely applied in 3C electronics, lithium batteries, electronic components, semiconductors, hardware, and other industrial manufacturing sectors.
Introduction to Motion Controller
It can perform complex motion control functions like linear interpolation and circular interpolation. It also handles continuous trajectory processing and supports IO high-speed latch input. Additionally, it offers precise output and position synchronization output (PSO). This makes it ideal for turntable visual screening equipment with 2-8 visual inspection stations.
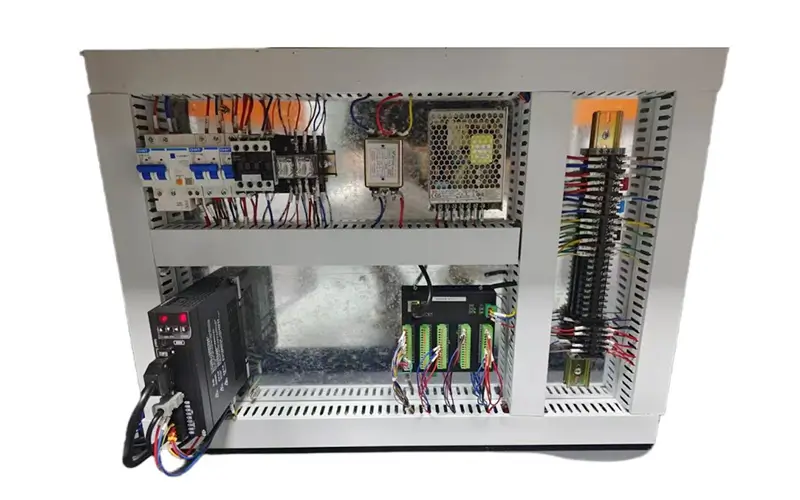
Advantages of controller application in turntable visual screening machine
- It can control the turntable in real-time and record the feedback position of the encoder;
- The high-speed input port connects to the sensor, sensing and recording the parts’ positions.
- The PSO hardware output connects to 2-8 cameras for visual flying, detection, and measurement.
- The PSO hardware output also connects to the airport for screening and classifying visual inspection results.
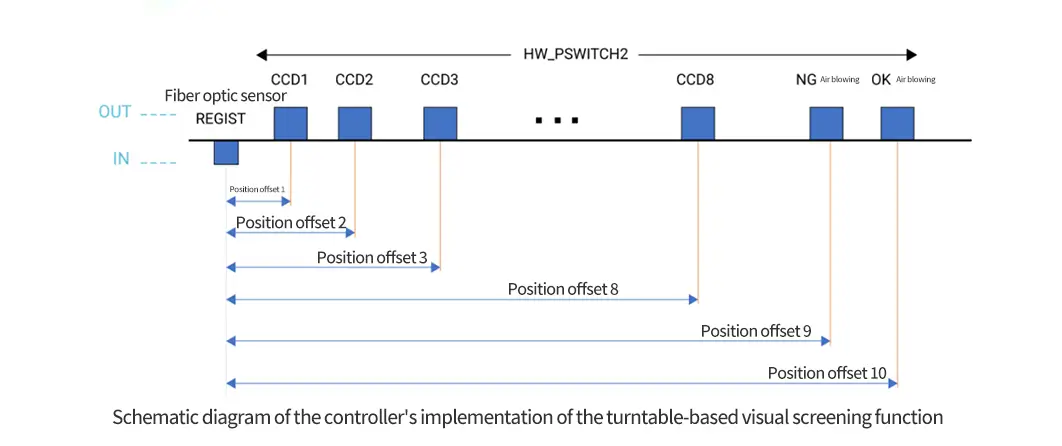
Principle of glass turntable visual screening machine
Working principle
First, the vibration plate transports the parts to the high-transparency glass turntable. Then, the sensor detects the incoming parts, and the controller records their position using the high-speed latch input port.
When the turntable reaches the visual inspection station, the controller triggers the camera to take pictures through the high-speed output port.
then performs image processing operations, and finally automatically detects and screens according to the preset inspection standards,
and rejects defective products.
Motion control system principle
Compared to the traditional PLC+touch screen solution, the motion controller-based system offers better integration, faster response, and higher efficiency.
When the glass turntable moves quickly, the hardware triggers the camera for visual shooting. It processes images and outputs screening results in real-time, greatly improving inspection speed.
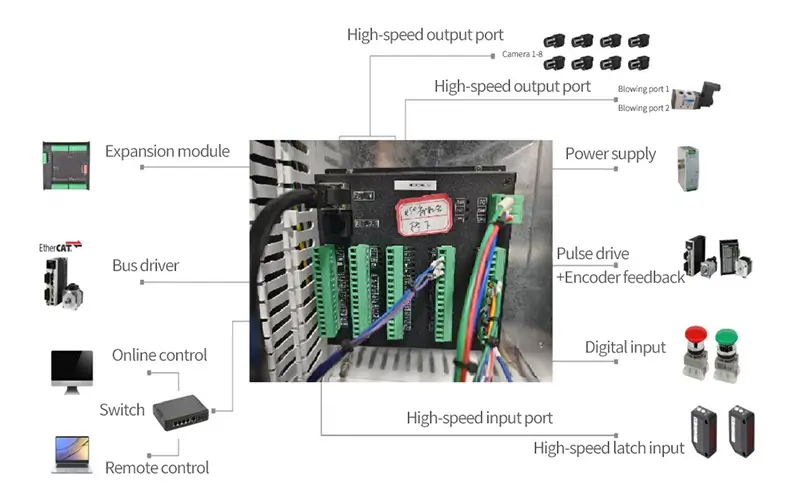
Visual system principle
The camera’s response time, exposure, pixels, and light source control must meet turntable speed requirements. This ensures that visual shooting, measurement, and inspection match the movement speed of different parts.
Application of motion controller and vision in turntable visual screening equipment
System action flow
- Inspectors load the products to be examined
Select the vibration plate based on the material type. The vibration plate transports parts to the high-transparency glass turntable. The turntable then rotates at a constant set speed.
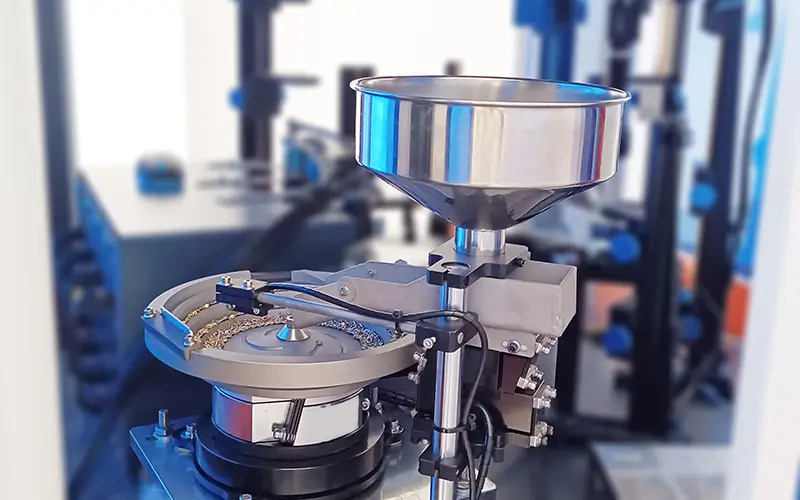
- Sensing materials and recording positions
When the sensor senses the material, the high-speed latch port based on the laser sensor records the current position of the material;
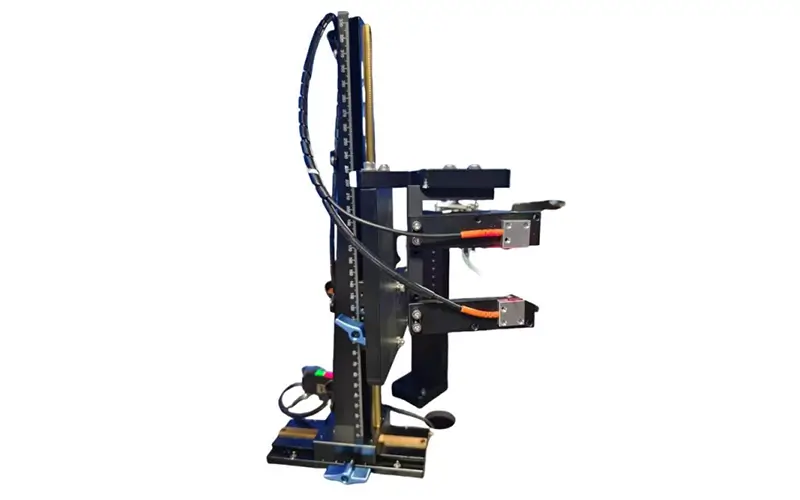
- Camera triggers photo shooting
The system calculates each camera’s position using the high-speed latch port. The motion controller’s hardware position comparison output then triggers the camera for visual flying shooting.
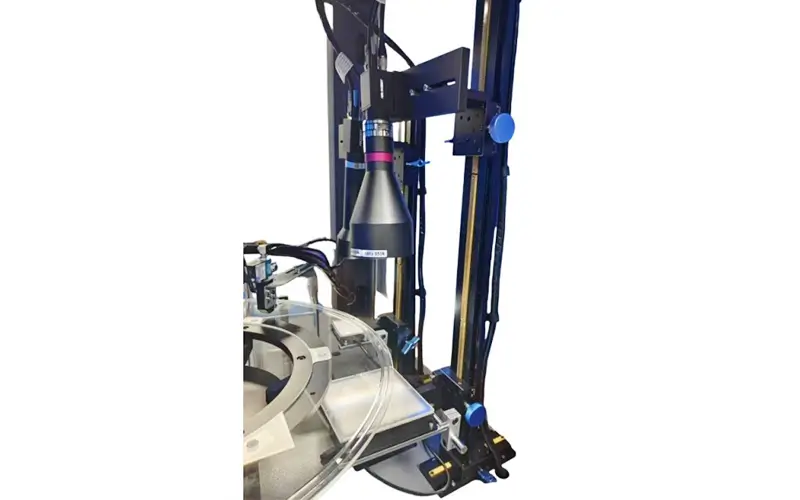
- Visual system processing
Perform visual inspection, measurement, recognition, and other functions on the photographed material images, and transmit OK or NG signals to the motion controller; air blowing screening.
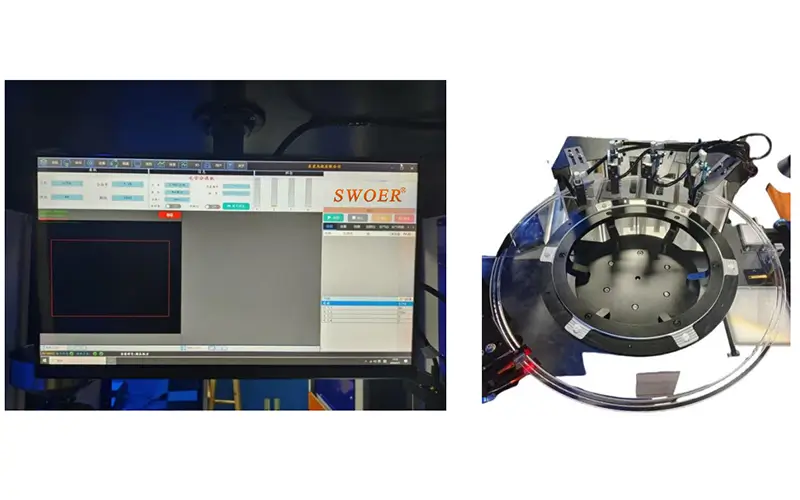
The visual system feeds back results to the motion controller, and the sensor provides the material’s position. The system calculates the air outlet position and uses the motion controller’s hardware position comparison output to control the air outlet for screening good and bad products.
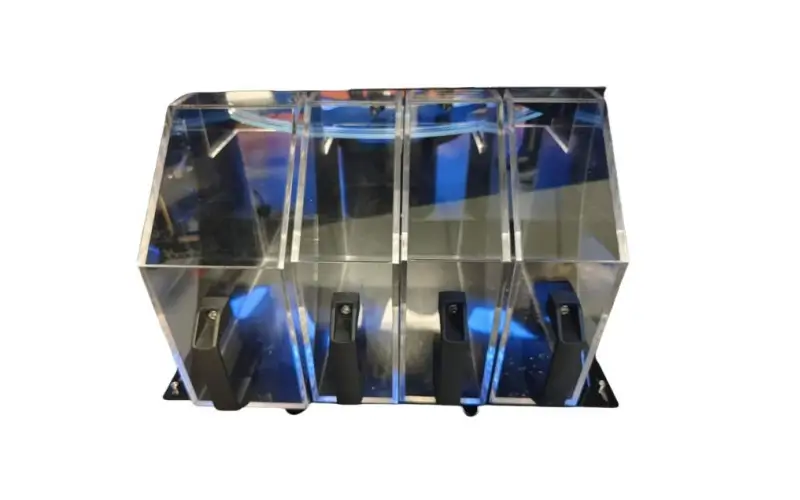
Solution Advantages
- Stable test results with high consistency;
- Automatically screen and classify defective products and remove them to improve product quality;
- Compared with static shooting, visual flying shooting reduces machine CT and improves efficiency;
- One person operating a machine can replace 2-6 manual operations and improve production capacity;
- Monitor each production inspection process to ensure it is reliable and effective.
- Compared with the traditional PLC+touch screen solution, it has higher integration, better cost performance, faster response and higher efficiency.
Reviews
There are no reviews yet.