In modern manufacturing, automated production lines have become the key to improving efficiency and accuracy. As a key component of automated production, you must seamlessly integrate the flex feeder into the automated production line. This article will explore how to achieve this integration and why it is essential for successful automated production.
Basic concepts of flex feeders
A flex feeder is a device for automated production. It efficiently transfers parts or materials from one place to another. The working principle ensures precise control of movement. Materials follow a predetermined path and speed.
Components of automated production lines
Automated Robotic Arm
Effect:
The robotic arm is primarily responsible for picking up materials in the flex feeder.It can accurately grab, transport, and place materials. This meets the needs of automated production lines. The flex feeder ensures precise material retrieval.
Features:
- Flexibility: The robotic arm has multiple degrees of freedom. It can perform precise picking operations. It works in multiple directions and angles.
- Accuracy: The high-precision control system ensures that the robotic arm can achieve accurate picking and placement of materials.
- Programmability: You can program and adjust the robotic arm according to production needs to achieve a variety of picking tasks.
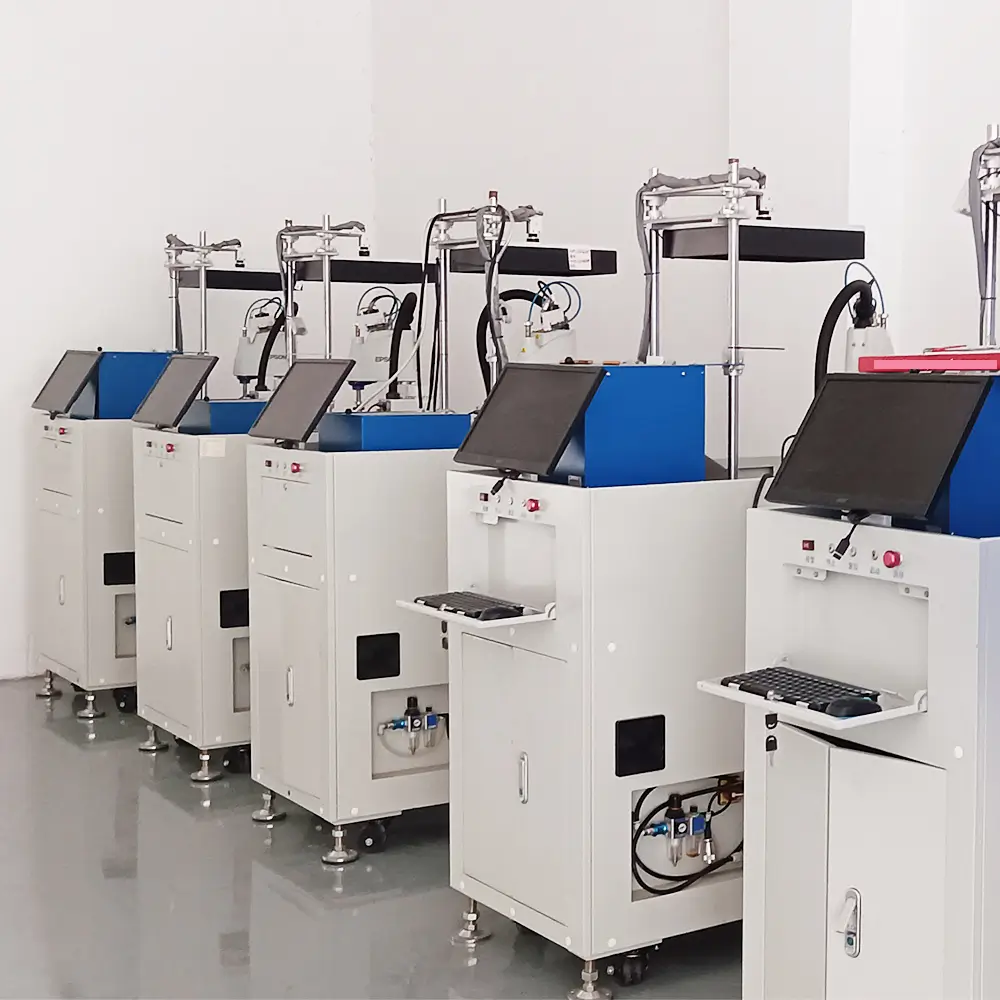
XY Module
Effect:
Similar to the robotic arm, the XY module is also a key component used for material-picking tasks. It provides a two-dimensional mobile platform. This ensures accurate movement and positioning of materials. The platform supports precise operation within the flexible feeder.
Features:
- Accurate positioning: The XY module enables high-precision material positioning. This ensures that materials move accurately to the target location.
- Smooth movement: Smooth motion control ensures the stability of materials during movement, reducing errors and damage.
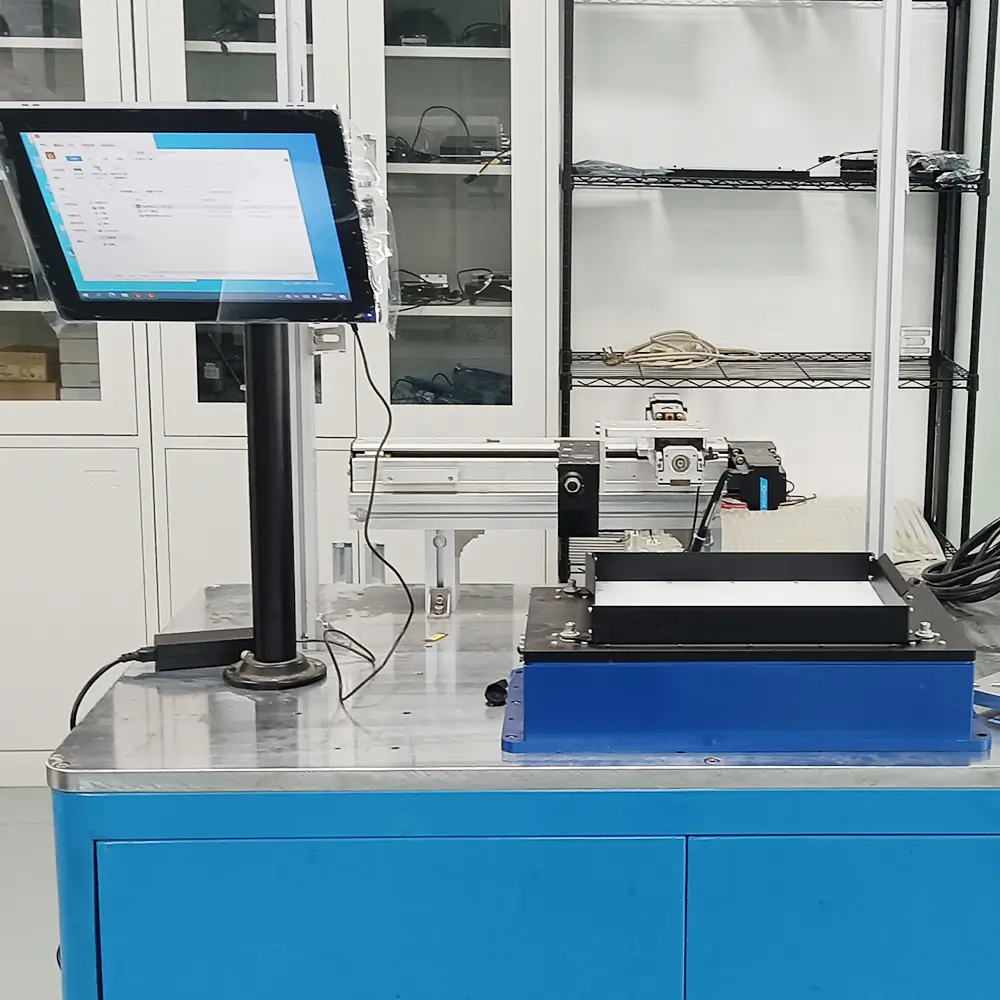
The difference:
- Price: The industrial robot arm is usually more expensive. Its higher flexibility and complexity increase the cost.
- Structure and design: Robotic arms have more joints and degrees of freedom. The XY module is primarily a flat moving platform.
- Application scope: Both can perform material picking tasks. The robotic arm suits complex, changeable environments. The XY module is better for simple, stable production tasks.
Overall, both the robotic arm and XY module are crucial for material picking in a flex feeder. Which one you choose depends on the complexity of your production needs, your budget, and other specific requirements. The robotic arm provides greater flexibility and complexity, while the XY module provides a more economical and stable solution.
Application of CCD Vision System
The CCD Vision System uses image recognition technology. It monitors and analyzes material location and status in real-time during production. It works in conjunction with other components to ensure the accuracy and efficiency of automated production lines.
In flex feeder systems, the robotic arm and XY module can combine with a CCD vision system. This enhances functionality and accuracy.
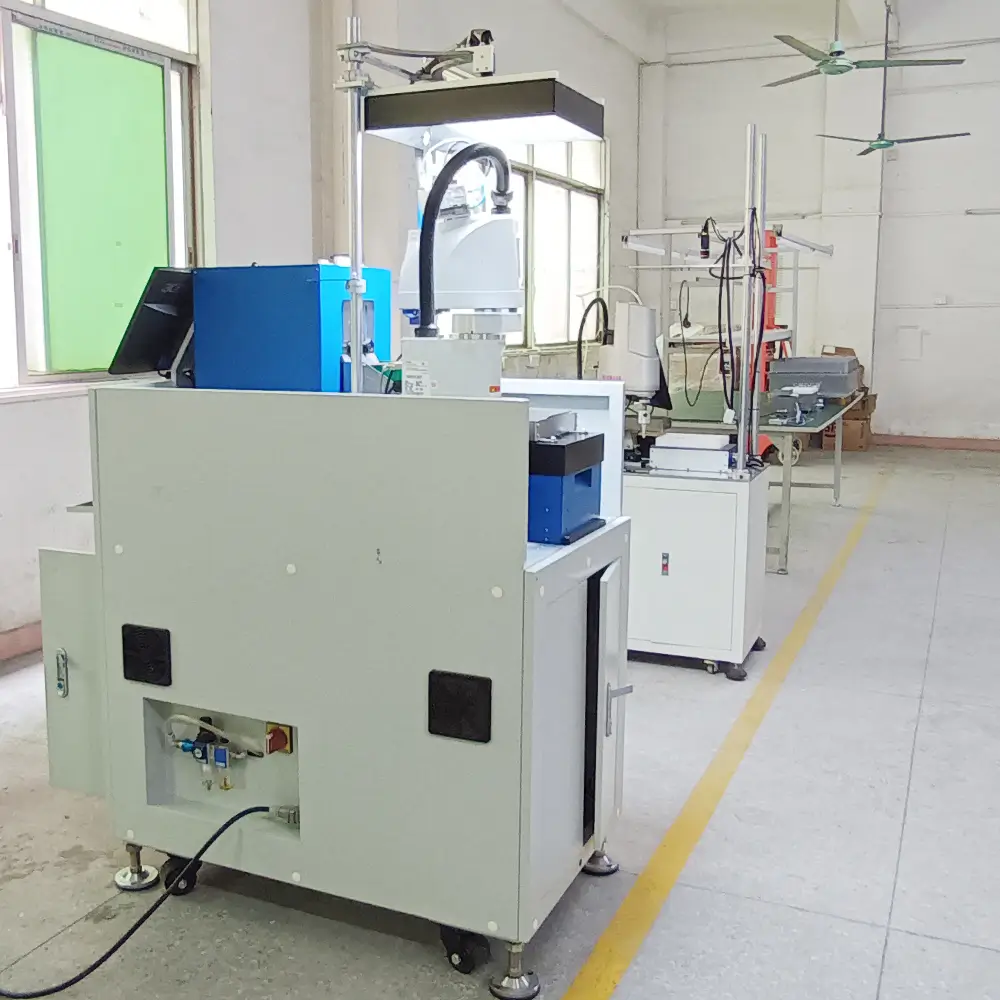
Combination of robotic arm and CCD vision system
When combined with a CCD vision system, the robotic arm achieves higher material identification and positioning. The CCD system captures real-time images of materials. It identifies location, shape, and status using image processing technology. This information can then be transmitted to the robotic arm, allowing it to perform more accurate pick and place operations.
Advantage:
- Enhanced accuracy: The CCD vision system provides precise material location information. This greatly improves the picking and placing accuracy of the robotic arm.
- Enhanced adaptability: The robotic arm adjusts in real-time using data from the CCD vision system. This helps it adapt to different production scenarios and material changes.
The combination of the XY module and CCD vision system
More precise material positioning and movement can be achieved after the XY module is combined with the CCD vision system. The CCD vision system offers precise location and direction information. It uses real-time image recognition technology. This guides the XY module to move and position materials accurately.
Advantage:
- Precise positioning: The CCD vision system provides high-precision material position data. This helps the XY module move materials accurately to the target location.
- Improve efficiency: With the CCD vision system, the XY module can position and move materials faster. This enhances production efficiency.
in conclusion:
In summary:
Whether it’s a robotic arm or an XY module, combining with a CCD vision system improves accuracy, efficiency, and adaptability. The CCD system provides key material information through real-time image analysis. This allows both systems to complete material handling tasks more intelligently and accurately. This combination provides strong support for automated production and helps companies optimize and improve their production processes.
Frequently Asked Questions
How to ensure compatibility between the Robotic Arm and flex feeder?
Ensuring compatibility of the Robotic Arm with the flexible feeder is key. This requires thorough research and testing before purchase. It ensures that communication protocols and operating methods are compatible.
What is the role of XY Module in the automated production line?
The XY Module provides a controllable moving platform for precisely positioning and moving materials. It ensures that materials can move accurately and efficiently through automated production lines.
How does the CCD Vision System enhance production efficiency?
Through real-time image analysis, the CCD Vision System quickly identifies and adjusts anomalies. This improves production efficiency and accuracy.